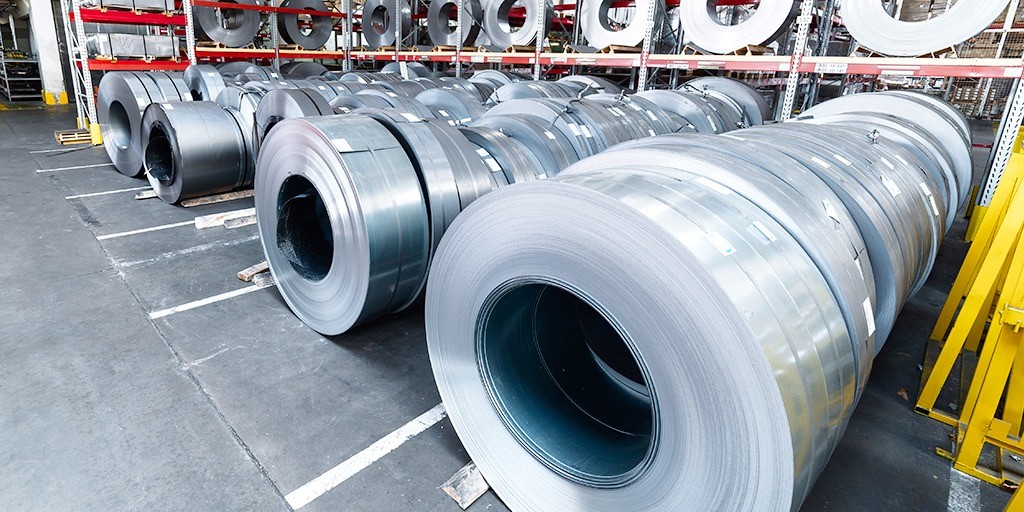
Understanding the Lifecycle of Aluminium
Aluminium has transformed industries and lives with its versatility, strength, and sustainability. From extraction to the final transformation into everyday products, aluminium undergoes an extensive lifecycle that exemplifies efficiency and environmental consciousness. Here’s a comprehensive look into the life cycle of aluminium and the value chain that makes it a critical part of modern living.
Bauxite Mining
The journey of aluminium begins with bauxite mining, the extraction of its primary ore. Bauxite, rich in aluminium content, is predominantly found in regions around the equator. Its abundance ensures a steady supply for generations to come. Mining processes have evolved, with increased emphasis on minimising environmental impact and restoring the land post-extraction.
Alumina Refining
Once bauxite is mined, the next step is refining it into alumina (aluminium oxide) through the Bayer process. This method involves crushing bauxite and treating it with a hot, pressurised sodium hydroxide solution. This dissolves the alumina and separates it from the impurities. After being separated and dried, the alumina is prepared for use in the manufacturing of aluminium. Because it changes bauxite into a condition that can be processed into primary aluminium metal, this refining process is essential.
Primary Aluminium Production
The conversion of alumina into aluminium metal involves electrolysis. The necessity of renewable energy sources in the aluminium sector is highlighted by the substantial quantity of power needed for this energy-intensive stage. Throughout the manufacturing lifecycle, firms are working to become carbon neutral by using green electricity.
Fabrication of Aluminium
Once primary aluminium is produced, it enters the fabrication phase, where it is transformed into products that can be used across various industries. Aluminium fabrication involves processes like extrusion, rolling, and casting, each adding distinct properties to the material.
Recycling
Aluminium is a star performer in recycling, requiring only 5% of the energy used in its primary production. This efficiency is paired with the metal’s unique ability to retain its properties through endless recycling cycles. An astonishing 75% of all aluminium ever produced remains in use today. Companies are increasingly focusing on recycling contaminated and post-consumer scrap, ensuring aluminium’s role in a circular economy.
At Shyam Metalics, we are proud to be at the forefront of this journey, reshaping and repurposing aluminium to meet the challenges and opportunities of our times. By leveraging innovation and sustainability, we ensure aluminium remains a cornerstone of a greener and brighter future.